Request for quote
To receive a quote please fill in this form below. One of our sales representatives is glad to help you.
Overview of 2-Stage Telescope Actuators
The 2-stage telescope actuator is a linear drive system, which offers the right solution for various application areas in mechanical engineering for large travels with limited spatial requirements.
The compact design elements of A.MANNESMANN offer small structural dimensions with the highest precision in performance.
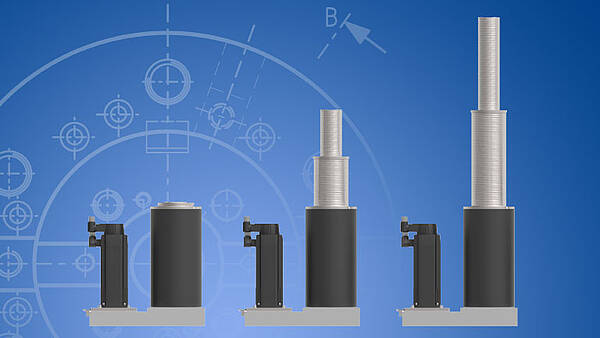
High Flexibility in Application
The linear actuator is a functional unit that can be used to implement demanding drive and positioning tasks. These tasks include displacement movements of components with complex, path-dependent processes as well as pressing and joining tasks with direct force-path evaluation.
Application Areas
The compressed design opens up a variety of opportunities. The 2-stage telescope actuators achieve both precise travel movements in machine tool precision as well as the high power transmissions that are required in press and jig construction.
2-stage telescope actuators are used in a variety of ways in mechanical and plant engineering where more space is required, such as in aerospace, special machine construction or process engineering.
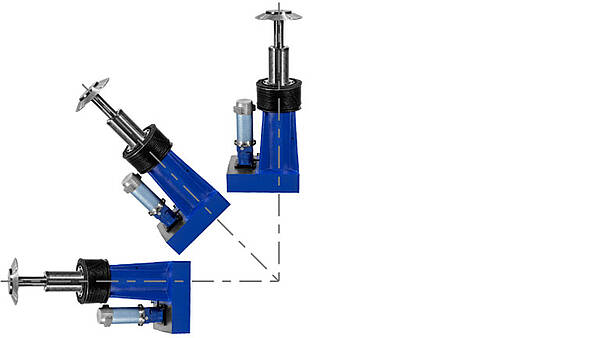
Advantages at a Glance
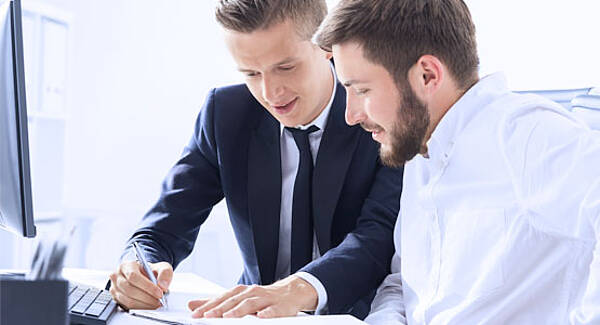
Economical advantages
- Space gain through compressed design
- High long-term durability / service life
- Economical standard designs or custom production
- Allows for compact mechanical engineering solutions in a small space
- Low power loss
- Excellent energy efficiency
- Maximum long-term precision
- Maximum possible machine availability
- Perfected wear resistance due to nitrided spindle
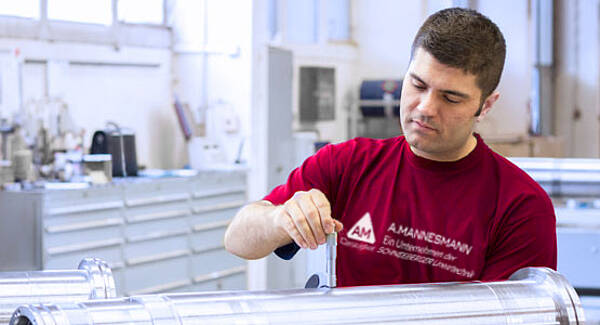
Technical advantages
- Small block dimensions
- Maximum positioning capability and repeatability
- Exact travel movements
- High rigidity
- Large travel (< 262%)
- Backlash-free, preloaded double nuts
- Ball screw spindles with ground precision (accuracy IT 3)
- Constant torque
- Very low power losses
- Uniformly low operating temperatures
- Can be used in all installation positions
- The highest power transmission rates
- Extremely high degree of efficiency (up to 98%)
Detailed Structure
The 2-stage telescope actuator is marked as follows:
- Telescopic ball screws
- Unilateral
- Compact design
- High extension ratio
- High effective pitch
- Central torque introduction
- Driven spindle
- Driven nut
In the event of a space gain of up to 262%, A.MANNESMANN telescope actuators work with large axial load capacity with extreme precision. The patented 2-stage telescope actuators convert the central rotatory drive motion of the motor into an axial translation movement through a telescopic ball screw.
Telescopic ball screws consist of two nested precision ball screws. The resulting partial movements split according to the thread pitches and occur absolutely synchronously.
The highest precision positioning and repeat accuracies are achieved through backlash-free, preloaded double nuts and ball screw spindles with ground precision in the accuracy quality IT 3.
High long-term durability is formed by perfect machining at A.MANNESMANN with high quality materials and heat treatment with the highest hardness.
The torque and the very high degree of efficiency of the telescopic levels of more than 90% are constant across the entire travel. Only in this way do very low power losses and evenly low operating temperatures result.
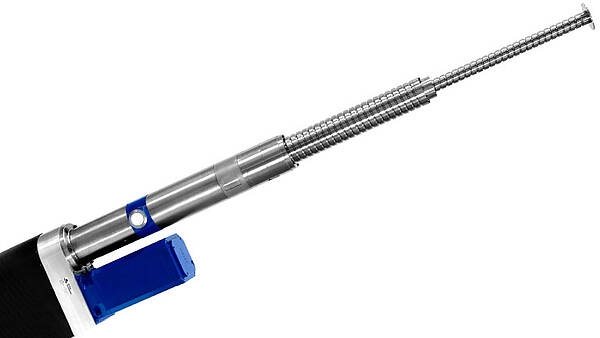
Standards and Custom-Made Production
We provide 2-stage telescope actuators in five standard sizes with different travel and axial forces in the tensile and compressive direction.
In addition, we produce your custom telescope actuators as special solutions with extensive accessories as part of our individual production. We precisely adapt the telescope actuators to your application conditions.
A.MANNESMANN Product Data
We will be happy to provide you with custom component drawings and dimensions of the 2-stage telescope actuators created according to your requirements after consultation for use in your CAD system to complete your planning documents.
Standard designs for 2-stage telescope actuators
Technical data | Type | Standard 1 | Standard 2 | Standard 3 | Standard 4 | Standard 5 |
---|---|---|---|---|---|---|
Installation size | mm | 32 | 40 | 50 | 63 | 80 |
Total pitch | mm | 10 | 10 | 20 | 30 | 40 |
Telescopic levels | 2 | 2 | 2 | 2 | 2 | |
Pitch per level | mm | 5 | 5 | 10 | 15 | 20 |
Ball size | mm | 3.5 | 3.5 | 6 | 8 | 10 |
Dynamic load rating | kN | 29 | 34 | 67 | 110 | 166 |
Static load rating | kN | 39 | 58 | 140 | 233 | 377 |
Max. dynamic axial load | kN | 6.4 | 7.6 | 18.8 | 35.6 | 59 |
Max. static axial load | kN | 10 | 14,5 | 35 | 58 | 94 |
Basic installation length | mm | 200 | 220 | 260 | 300 | 350 |
Max. travel | mm | 1,000 | 1,500 | 2,000 | 2,500 | 3,000 |
Min. installation length * | mm | 700 | 970 | 1.260 | 1.550 | 1.850 |
Max. installation length* | mm | 1,700 | 2,470 | 3,260 | 4,050 | 4,850 |
Extension ratio* | 2.43 | 2.55 | 2.59 | 2.61 | 2.62 | |
Positioning accuracy | μm | 16 | 16 | 16 | 16 | 16 |
Max. operating speed | rpm | 1,500 | 1,500 | 1,200 | 1,000 | 800 |
Max. travel speed | m/min | 15 | 15 | 24 | 30 | 32 |
* in relation to the max. travel |
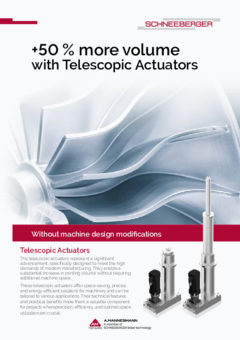
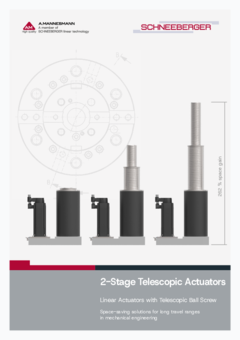
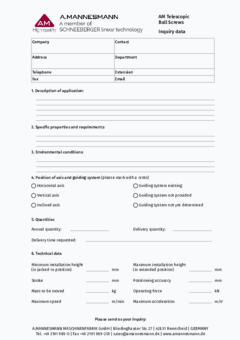