Es ist ein Weg ohne Wenn und Aber
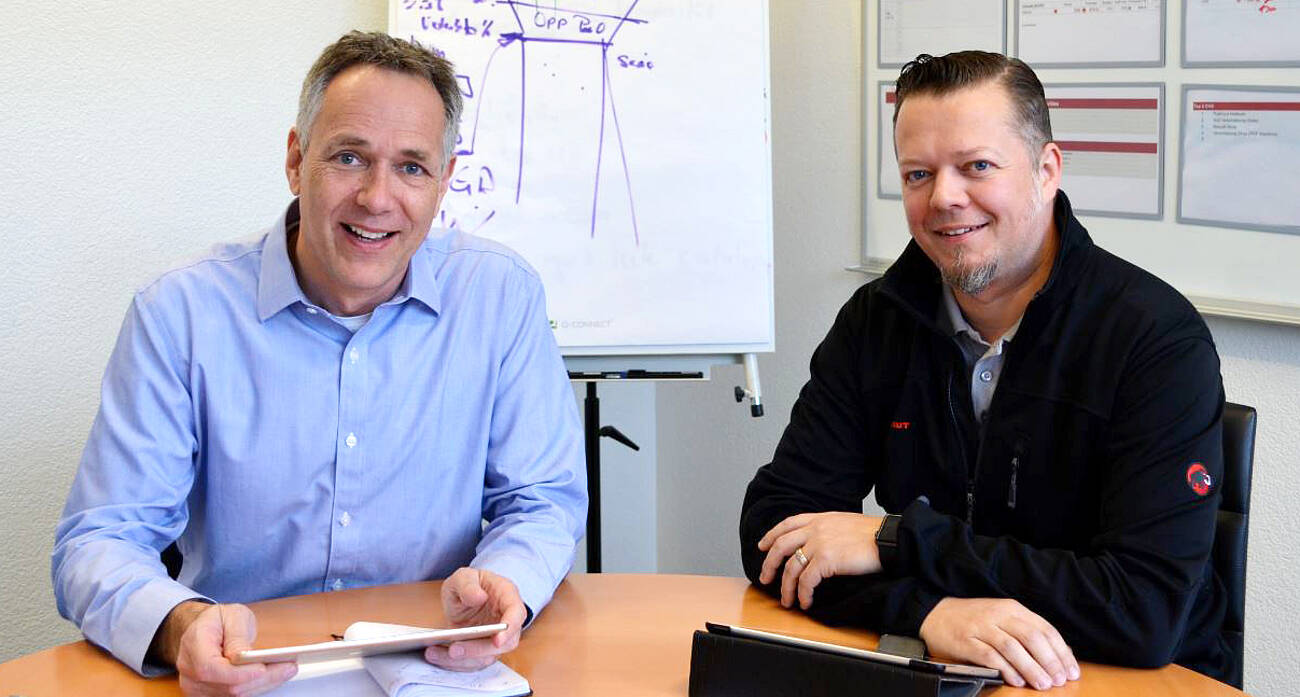
Mit der Einführung eines Lean-Managementsystems hat sich die Schneeberger Lineartechnik AG fit gemacht für die Zukunft. Dass diese Massnahme geholfen hat, den 15. Januar 2015 genauso abzufedern wie eine konjunkturelle Delle im vorigen Jahr, verdeutlicht die Bedeutung schlanker Prozesse. Im TR-Interview geben Adrian Fuchser, Geschäftsführer der Schneeberger AG, und Yves Breitschmid, Manager Lean Programm, Auskunft über die Bedeutung von Lean Management und dessen durchaus anspruchsvolle Umsetzung.
Herr Fuchser, die Schneeberger AG beschäftigt sich seit 2013 mit dem Thema Lean Management. Wie sehr hat Ihnen die Verschlankung der Prozesse geholfen, den Frankenschock vom 15. Januer 2015 zu verdauen?
Fuchser: Wir haben gegen Ende 2013 angefangen, Lean einzuführen, und da war weder die Aufhebung der Währungsuntergrenze ein Thema, noch, dass wir 2016 mit einem deutlichen Umsatzrückgang in einem unserer Geschäftsfelder zu kämpfen haben werden. Wir sind froh, haben wir bereits zuvor damit begonnen, denn es ist ganz klar: Unsere Lean-Aktivitäten haben dazu beigetragen, diese beiden Ereignisse relativ unbeschadet zu überstehen.
Gibt es dazu ein paar konkrete Zahlen?
Fuchser: Im Geschäftsfeld Halbleiterindustrie mussten wir im vorigen Jahr einen Umsatzeinbruch von fast 40 Prozent hinnehmen. Glücklicherweise konnten wir bereits 2015 im selben Bereich aufgrund Lean-Massnahmen die Margen bei einem durchschnittlichen Umsatz um 40 Prozent steigern. Das hat uns natürlich extrem geholfen. Zudem haben wir seit 2014 Arbeit, die extern vergeben war, sukzessive wieder ins Haus holen können, auch aufgrund unserer Lean-Aktivitäten. Das war ein wichtiger Schritt zur Sicherung von Arbeitsplätzen.
Breitschmid: Wir konnten in den letzten beiden Jahren viele Projekte umsetzen, die im magischen Dreieck Qualität, Kosten und Liefertreue zu deutlichen Verbesserungen der Prozesse geführt haben. Dazu gehört, den Begriff der Verschwendung deutlich zu machen. Denn nicht jeder, der in hektische Betriebsamkeit verfällt, ist auch wertschöpfend tätig. Es ist auch nicht gegeben, dass jeder, der von Verschwendung spricht, dasselbe versteht wie der, der zuhört. Die Änderung dieser Sichtweise ist fundamental.
Gab es einen konkreten Anlass, sich mit Lean Management zu beschäftigen?
Fuchser: Ich habe vor rund fünf Jahren die Geschäfte bei Schneeberger in Roggwil übernommen, davor war ich für die Niederlassung in den USA verantwortlich. Bei der Analyse der Schweizer Geschäftszahlen sind wir damals auf einen Negativtrend von Wertschöpfung zu Personalkosten gestossen. Wir mussten also handeln, auch deshalb, weil wir mit bestimmten Produkten immer schon in einem volatilen Markt unterwegs sind. Gleichzeitig war uns bewusst, dass wir technologisch gesehen unsere Prozesse eigentlich im Griff hatten, der reine Workflow war die Herausforderung. Und so sind wir nach und nach in das Thema Lean hineingerutscht, bis wir uns 2013 entschieden, mit einem externen Partner das Thema ernsthaft anzugehen.
Welche Hauptstossrichtung hatten Sie damals definiert?
Fuchser: Unser Fokus lag darauf, mit schlanken Prozessen die Gesamtprozesszeit deutlich zu verbessern. Das bedeutet wiederum, je weniger Verschwendung, desto tiefere Kosten. Um die Durchlaufzeiten zu reduzieren, die es braucht, um ein Produkt vom Rohmateriallager bis zur Spedition durchzuschleusen, haben wir nicht nur die reine Maschinenproduktivität in Betracht gezogen, sondern sämtliche Faktoren, die einen Einfluss auf die Zeit haben. Diese sind zum bedeutet wiederum, je weniger Verschwendung, desto tiefere Kosten. Um die Durchlaufzeiten zu reduzieren, die es braucht, um ein Produkt vom Rohmateriallager bis zur Spedition durchzuschleusen, haben wir nicht nur die reine Maschinenproduktivität in Betracht gezogen, sondern sämtliche Faktoren, die einen Einfluss auf die Zeit haben. Diese sind zum Beispiel die Prozessstabilität, Liegezeiten vor Maschinen und Zeiten für Nacharbeit fehlerhafter Teile. Diese Verkürzung der Durchlaufzeit hilft uns wiederum agiler zu werden, um schneller auf Veränderungen reagieren zu können.
Breitschmid: Allerdings hat sich das in der Realität nicht so einfach dargestellt. Denn der Gewinn an Schnelligkeit ging teilweise wieder verloren. Das heisst, punktuelle Verbesserungen sind noch nicht das Ende der Reise. Bis die positiven Effekte sich in den Büchern wirksam zeigen, benötigt es die Verkettung der Optimierungen. Habe ich dank einer Optimierung eine hocheffektive Maschine, welche mir jedoch den Puffer zur nächsten Maschine füllt, da diese nicht nachkommt, hat sich die erste Optimierung für sich noch nicht gelohnt. Hinzu kommt, dass bei einer «überhasteten» Einführung von Lean-Methoden wie Kanban oder geglätteter Fertigung Vorsicht geboten ist.
Fuchser: Wir haben also festgestellt, dass wir mit dem Lean-Ansatz deutlich weiter vorne im Prozess beginnen müssen. Einer der ersten Schritte ist es, stabile Prozesse zu haben. Es ist kontraproduktiv, einzelne Abläufe schneller machen zu wollen, wenn man die eigentlichen Produktionsprozesse nicht im Griff hat.
Ist es deshalb so wichtig, einen externen Berater mit ins Boot zu holen?
Fuchser: Wir sind auf einem so tiefen Niveau gestartet, da wäre es ohne externe Hilfe schwierig gewesen, überhaupt voran zu kommen. Mit der Noventa Consulting AG hatten wir einen Partner, der uns viele wertvolle Anregungen gegeben hat. Wir wussten von Anfang an aber auch, dass wir zweigleisig fahren wollen. Im ersten Schritt mit Hilfe von aussen, um die weiteren Schritte dann intern begleiten zu können. Deshalb haben wir Herrn Breitschmid eingestellt, der sich ausschliesslich um das Thema Lean kümmert.
Breitschmid: Wobei Consulting nicht gleich Consulting ist. Richtig gute Berater vermitteln in ihren Workshops zehn Prozent Theorie und 90 Prozent Praxis. Es ist für einen Berater von Vorteil, wenn er die Erfahrungen, die er weitergibt, auch bereits selbst erlebt hat.
Fuchser: Der Vorteil dieses praxisorientierten Ansatzes ist, dass innerhalb von ein paar Tagen bereits sehr konkrete Ergebnisse zu sehen sind, und die Akzeptanz der Lösung bei den Betroffenen deutlich höher ist.
Wie kann ich mir so eine Umsetzung vorstellen?
Fuchser: Ein Workshop-Team analysiert meist an einem Tag einen Arbeitsplatz, legt anschliessend zwei Tage selbst Hand an bei der Umsetzung der Optimierung, dann wird das Ergebnis begutachtet. Wenn die Prozesse dann plötzlich 40 Prozent schneller ablaufen, braucht man nicht mehr viel zum Thema Lean zu sagen. Das erklärt sich dann von selbst.
Breitschmid: Nicht umsonst sind alle Lean-Arbeitsplätze in der Montage von den Mitarbeitern selbst aufgebaut worden und werden auch laufend verbessert.
In welchen Abteilungen hat man mit der Lean-Einführung begonnen?
Breitschmid: Wir haben mit der Montage angefangen und dann auf Empfehlung von Noventa relativ schnell mit der Produktion weitergemacht. Man beginnt mit der Einführung eigentlich immer dort, wo man den grössten Handlungsbedarf sieht und die grösste Kundennähe herrscht. Anschliessend arbeitet man sich nach und nach an das andere Ende respektive den Anfang der Prozesskette vor. Das ist insofern sinnvoll, weil dadurch alle Verbesserungsschritte aufeinander aufbauen, und man nicht aneinander vorbei optimiert.
Fuchser: Natürlich gibt es in den verschiedenen Abteilungen unterschiedliche Optimierungsgeschwindigkeiten. Es ist beispielsweise nicht so einfach, den Workflow in der Produktion zu optimieren. Die Prozesse dort sind komplexer, vielleicht auch weniger durchschaubar. Hier mussten wir viel mehr im Team arbeiten.
Mittlerweile, das heisst, rund zwei Jahre nach der Lean-Einführung, ist man bereits durch alle Abteilungen gegangen, bis hin zur Konstruktion und zum Engineering. Das ist sportlich.
Breitschmid: Stimmt, ein solches Tempo ist eher selten der Fall. Diese Vorgehensweise hat uns Noventa aufgrund ihrer Erfahrungen empfohlen. Es ist ein sehr beachtenswerter Aspekt bei Schneeberger, dass man diesen Sprung quer durch alle Abteilungen bereits in einem sehr frühen Stadium mitgemacht hat.
Fuchser: Wobei man ehrlicherweise sagen muss, dass nicht jede Abteilung gleich weit in der Umsetzung ist. Sehr positiv finde ich allerdings, dass die Abteilungen den Sinn der Massnahmen erkennen und bemüht sind, die Lean-Einführung zu unterstützen, egal, ob es sich um die Produktion, Buchhaltung oder das Personalwesen handelt. Der Weg dahin kann dann durchaus ein längerer sein.
Apropos Sinnhaftigkeit: Wie wichtig ist bei einer Lean-Ein-führung die Kommunikation durch das Management an die Mitarbeiter?
Fuchser: Ich denke schon, dass es ein nachhaltiges Element war, dass die Mitarbeiter gesehen haben, wie intensiv sich das Management um diesen Prozess bemüht hat und auch erste Schritte gegangen ist. Mindestens genauso wichtig ist, dass Mitarbeiter früh über den gesamten Einführungsprozess informiert werden. Denn jede Veränderung stösst erst einmal auf Skepsis. Das war bei uns genauso. Irgendwann wollen dann alle die Veränderung, weil man sieht, was sie bewirken kann. Aber die erste Schritte fangen immer bei einem selbst an.
Breitschmid: Das gilt gerade für die Kader und das Management. Wenn man ernsthaft den Anspruch hat, Lean Management in die Unternehmenskultur zu verankern und als Philosophie zu begreifen, dann muss die Führungsebene die Bereitschaft signalisieren, durch Lean freigewordene Kapazitäten nicht zum Stellenabbau zu nutzen, sondern durch Aufträge zu füllen. Wenn das nicht funktioniert, dann ist Lean nach dem dritten oder vierten Workshop gestorben.
Das heisst: Lean Management sollte nicht als Instrument für Rationalisierungsmassnahmen gesehen werden?
Breitschmid: Das ist ein Killerargument. Bei Lean geht es immer um Prozessoptimierung und nie um Rationalisierung. Sollte also ein Unternehmen in wirtschaftlich turbulenten Zeiten diesen Schritt gehen wollen, empfehle ich, zuerst ein Projekt aufzugleisen, das sich mit dem Turnaround beschäftigt. Ist das abgeschlossen, kann man in die Diskussion einsteigen. Beides zu verquicken, also Rationalisierung und Lean, halte ich für nicht zielführend und rückt die Bestrebungen nur in ein falsches Licht.
Fuchser: Wir haben im Rahmen der Lean-Einführung auch noch andere Unternehmensziele formuliert. Eines davon war ein ganz klares Wachstumsziel.
Welche Stolpersteine gibt es noch auf dem Weg zu einer Lean-Umsetzung?
Fuchser: Lean ist kein Projekt, sondern ein Programm. Und dieses Programm umzusetzen, diese Kultur im Unternehmen zu implementieren, verlangt eine grosse energetische Leistung. Wenn man diesen Prozess unterschätzt, gerät man zum ersten Mal ins Stolpern. Die zweite Hürde, die es zu überspringen gilt, ist, die Mitarbeiter für diesen Weg zu begeistern. Erst wenn die Mitarbeiter erkennen, dass es Management und Kader mit der Lean-Einführung ernst ist, kann man erfolgreich sein.
Breitschmid: Ebenfalls ein No-Go ist die persönliche Ansprache in Form von Schuldzuweisungen. Lean ist eben anders, da geht es um Verschwendung im Prozess, und das muss jeder erst einmal lernen. Deshalb ist es mitunter wichtig, am Anfang mit externen Beratern zu arbeiten, die dieses Gefühl vermitteln können.
Fuchser: Die Botschaft der ersten Minute muss lauten: «Wir haben in der Vergangenheit nichts Schlechtes gemacht.» Aber wir wollen jetzt etwas anders machen und dadurch die Weichen für die Zukunft stellen. Dazu gehört auch, eine gewisse Fehlerkultur zuzulassen. Da Fehler in unserer Kultur per se negativ besetzt sind, gerät man mit der Lean-Einführung automatisch in einen Zielkonflikt. Denn wenn man etwas verändert, tauchen automatisch Fragen nach dem früheren, mithin fehlerbehafteten Verhalten auf. Das will niemand. Lieber arbeitet man dann ein wenig schneller, nur um zu zeigen, dass es auch so geht. Dieses Verhalten führt aber letztlich nicht zum Quantensprung, der das Unternehmen weiterbringt, wie es bei Lean der Fall ist.
Wo steht Schneeberger jetzt, zwei Jahre nach Lean-Einführung?
Fuchser: In der praktischen Umsetzung haben wir einen Status erreicht, um keine grosse Überzeugungsarbeit mehr leisten zu müssen, wollen wir Projekte anstossen. In Bezug auf die Unternehmenskultur dauert dieser Prozess wesentlich länger. Wir sind hier auf gutem Kurs, aber immer noch auf der Reise.
Breitschmid: Man darf nicht vergessen, dass die ganz grossen Würfe mit 30, 40 oder noch mehr Prozent Einsparungspotenzial meist am Anfang der Optimierungen stehen und dann immer seltener werden. Dies ist üblich; das Management muss sich dessen jedoch bewusst sein. So kann es ab dann das Vorgehen unterstützen, dass jeder Mitarbeiter in der täglichen Routine nach Verbesserungen und Verschwendung Ausschau hält. Das ist nicht sexy und kann auch nicht mit grossem Trara nach aussen kommuniziert werden. Aber diese kleinen Puzzlesteine führen in Summe zum grossen Ganzen.
Wie geht es jetzt eigentlich weiter?
Fuchser: Wir haben für die Abteilungen Roadmaps definiert. Unter anderem möchten wir die Fertigung wertstofforientiert umstellen. Die Maschinen werden nicht nach Fertigungsschritten wie Drehen oder Fräsen, sondern nach Produktgruppen organisiert. Das wird die kommenden Maschineninvestitionen prägen.
Gibt es eigentlich bereits ein Produkt, das rein auf Lean-Prinzipien entsteht?
Fuchser: Jein. Bei den kundenspezifischen Lösungen haben wir bereits auf allen Stufen den Lean-Ansatz angepackt. Ich sehe allerdings noch Optimierungspotenzial in der Konstruktion. Deshalb das Fragezeichen.
Breitschmid: Zu sagen, wir beginnen beim Verkaufsgespräch und ziehen den Lean-Ansatz über die Konstruktion, Arbeitsvorbereitung, Produktion, Montage bis zum Aftersales durch – so weit sind wir sicherlich noch nicht. Aber das ist ganz klar das grosse Ziel.
Hand aufs Herz: Ist alles so eingetreten, wie man sich das vorgestellt hat?
Fuchser: Man muss es vielleicht anders sehen, Herr Pittrich. Für uns war und ist es ein Weg ohne Wenn und Aber. Denn ich wüsste nicht, wo das Unternehmen heute stehen würde, wenn wir diesen Schritt nicht getan hätten. Wir haben einen Turnaround einleiten können, um auf einer ganz anderen Basis die Kostenkontrolle im Griff zu haben. Wir hätten den 15. Januar nicht so gut verdaut, und wir hätten auch den Umsatzrückgang im vorigen Jahr nicht so leicht wegstecken können. Durch Lean Management sind wir jetzt viel besser positioniert. Dazu passt auch, dass wir im Januar einen Auftragseingang hatten, wie ich ihn noch nie erlebt habe, seit ich bei Schneeberger bin.