Ball Screw Nuts - the Functional Guarantors
The ball nut is the most complex component of the ball screw assembly. The perfect functioning of the ball screw depends especially on the ball nut, as it contains the ball bearings, the ball return units and the wipers. The preload is generated via the nut if necessary, which on the one hand serves to avoid backlash and on the other hand increases the rigidity.
The Highest Demands on the Material and Design of the Nuts
As the ball nut not only carries rolling motion of the balls in the ball-track, but also in the ball return, it is subject to a constant load, unlike the screw. The operating temperature on the nut surface is therefore always slightly higher (about 5K) than the temperature on the screw surface. So that the ball nut can safely bear the high load over its entire service life, the nut is normally made of high-quality ball bearing steel (100Cr6) and is through-hardened.
If the screws are always custom-made due to the required stroke lengths, the ball nuts may be subject to a certain dimensional standardization. This may be done in the dimensions according to DIN ISO 3408 or DIN 69051 or also specific to the manufacturer. However, some ball nuts, which meet these requirements, are custom special components in many applications.
Requirements for Different Nut Designs
Despite all efforts for standardization, there are different nut designs depending on the requirements and installation situation. The first distinguishing criterion for ball screw nuts is the number of nut body parts. A distinction is made here between single nuts and double nuts. However, more than two nut parts may be necessary for a nut system due to the technical manufacturing needs.
Double Nut or Double and Triple Nuts
The double nut is the traditional nut design that is very popular, especially in machine tool design, as preloaded systems with 2-point contact are used here almost exclusively. Both ball nut parts are mounted so that the balls are clamped between the ball raceways of the spindle and the nut. The axial displacement is provided by ground intermediate washers or by twisting the nut parts to each other. In both cases, the distance between the loaded turns of both ball nut parts is increased or decreased.
The double nut is the traditional nut design of a ball screw. It normally consists of two parts, whereby one part (as a load carrying ball nut) absorbs the external load and the other ball nut part (as the preload nut) generates the preload. The load nut is always the ball nut part through which the axial force is guided into the direct distribution of forces.
Depending on the distribution of forces, O or X-preloads can be generated in a double nut. For technical production reasons, the ball nut parts can also be designed as two parts when it comes to double nuts so that a three-fold or four-fold ballnut is also possible.
The double nut can be designed both as a cylindrical nut as well as a flange nut. Both nut parts are geometrically identical with the cylindrical nut. The preload is then externally applied as an X-preload over at least one spacer.
With the flange nut, a distinction is made between the component with the flange and the lock nut (without flange). The preload is then always generated from the inside as an O-preload through the axial displacement of the loaded turns. This displacement may occur both via intermediate rings as well as through the distortion of the nut parts.
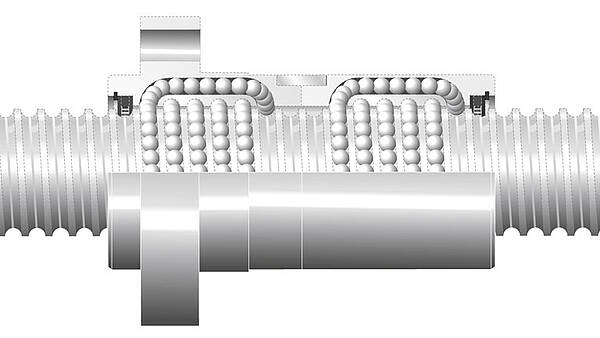
Single Nuts
The single nut is the most compact and lowest cost nut design. This is why it is very widespread and only consists of a nut body part with a continuous ball-track. In the simplest design, single nuts have a slight axial clearance.
Backlash-free preloaded single nuts are also possible by varying the loaded turns and/or a ball sizing as well as the structural design. Due to the imperfect running behavior of these designs, the preload is usually associated with increased friction, increased operating temperature and increased wear. Single nuts with preload are slightly more sensitive to production tolerances so that very long spindles are normally not equipped with preloaded single nuts. This does not apply to single nuts without preload, since they always run in 2-point contact under axial load. For single nuts with a 4-point contact, there cannot be ball relief during load peaks and therefore there cannot be sliding balls, since the load transfer and the preload occur via the same balls.
Preload through Ball Selection
The easiest way to eliminate play in a single nut is to use ball selection. These balls are larger than the gap between ball nut and screw, which is determined by the four ball raceway edges on the spindle and in the nut. The balls must be placed under force into this gap that is too small. 4-point contact exists due to the elastic flattening on the balls and in the ball raceways. Since DIN ISO 3408 does not apply as a basis for calculation for 4-point contact, the preload size must be determined empirically.
The amount of the preload is not variably adjustable with ball selection, but rather depends solely on the excess size of the balls and requires that the prescribed thread design is precisely achieved by production. The structurally specified locations of the ball support points must also be achieved during assembly. Only then is the preload force detectable and present in the single nut.
Preload through Pitch Offset
For two or multi-circuit ball nuts, the preload can also be achieved with single nuts through the pitch offset of the thread pitch between the individual circuits in the ball nut. Due to this offset, the balls in each circuit run independently of each other on a different edge of the spindle thread. The preload occurs through the ball on both edges in 2-point contact. The preload size is determined by the manufactured pitch offset. The preload can be modified through an additional ball selection.
Preload through Thread Shifting
Thread shifting is also possible in the nut to be able to preload single-run ball screws. In this process, the middle loaded circuit is produced with a steadily increasing lead shift. The balls thus run on one edge of the thread, with play in the middle and then switch to the opposite edge. The preload also occurs here through the balls on both edges in 2-point contact. The preload size is determined by the manufactured shifting. The fine tuning of the preload can also be done through ball selection.
Preload through Slotted Nuts
Another way to make backlash-free single nuts is axial slitting and twisting of the nut body. The width of the slit in the nut body is changed by a clamping screw. This reduces the ball track diameter, resulting in a preload with 4-point contact when combined with ball selection. However, in addition to the ball track geometry, the roundness in the nut thread also changes so that the preload and the running behavior of each ball are not constant and uniform.
Different Nut Designs
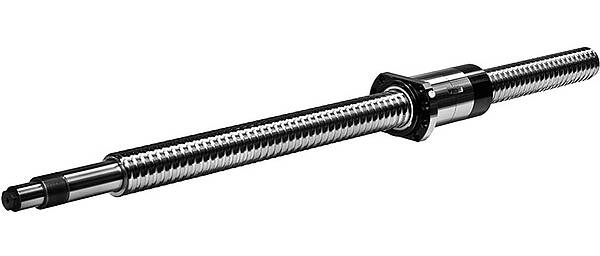
A second distinguishing criterion is the outer contour or the fastening type of the nut. In addition to the cylindrical design, the flange design is also important.
The two nut body parts must always be mounted in a housing for the preloaded cylindrical design via a double nut. The preload then occurs from the outside to the inside via pressure flanges. The preload is limited via a spacer between the nut parts. An X-preload always results here.
The mounting flange is always a fixed component of the nut body with flange designs (with side or middle flange). The preload is generated via the lock nut part by twisting both nut parts towards each other or via an adjustable intermediate washer from the inside to the outside. The lock nut is only held in the ball raceways by the balls and the applied preload force. The adjustment of the variable preload force is an individual assembly process, which can be very well matched to the application case and creates optimal conditions for high load capacity and long durability.