Ball Screw Spindle as a Load-Bearing Component
The ball screw spindle is the component part of a ball screw assembly that carries the nut. It is a cylindrical shaft and generally consists of at least two sections. One section bears the helical ball track through which the movement kinematics of the ball screw are implemented in its full length. The spindle thread is always loaded only sequentially (partially, temporarily) in the current ball contact area. The support bearing and possibly the drive connection are located on the other section(s). The forces and torques in the ball screw are introduced into or dissipated in the machine environment.
Influence of Spindle Length and Execution
The thread length of the spindle is normally determined by the active travel of the application, the total length of the nut (including the wiper system and other accessories) and the thread runout. Depending on the length and design, the ball screw spindle is mounted on one or both sides so that the entire length of the ball screw spindle may be significantly longer in parts than the thread length. The entire spindle length and the structural bearing design are crucial for the buckling and rotational stability and thus for the speed and load-dependent applicability of the ball screw.
The A.MANNESMANN ball screw spindle precision-ground in very close tolerances (IT 1, IT 3, IT 5) is produced from high-strength nitrided steel, whereby the entire ball screw form is deep-nitrided. It has a tough spindle core and a surface hardness of app 900 HV (= 67 HRC) with a hardening depth of at least 0.4 mm. This very high surface hardness is the basis for a high load capacity and a long service life.
Structural Determination
The structural determination of the spindle design is usually done by the user of the ball screw. It depends greatly on its task and the machine environment. The influence of A.MANNESMANN as a ball screw manufacturer is therefore usually focused on optimizing the function and production possibilities as well as on ensuring the quality required by the user.
The ball screw spindle is characterized by the thread diameter, thread pitch, pitch direction, ball size, thread length, accuracy class and by the thread profile and number of runs of the ball screw. The dimensioning and design of the support bearing and drive connection depend on the usual dimensions of the bearing types and their mounting needs or on the shaft-hub connections of the drive elements.
A spindle standardization is nearly impossible due to this individual design.
Different Spindle Designs
The structural design and geometric implementation result in some basic spindle versions that are not only technically very different from each other, but also are economically very different from each other. The individual distinguishing features are sometimes very significant, but are not always directly obvious.
Regardless of whether the ball screw spindle is designed to be driven or non-rotating, certain functional or production reasons may require special designs that do not correspond to a "normal" solid spindle. These include spindle designs such as:
- Hollow spindles
- Spindles with collars
- Coupled spindles
- Corrosion-resistant spindles
So that these ball screw spindles can also be produced in high quality, sometimes very different specific influences must be taken into consideration when producing ball screw spindles in special designs in addition to taking the already necessary care. Certain design-related limitations may occur when using such ball screw spindles.
Solid Spindles
Most ball screw spindles are designed as solid spindles. The spindle cross section corresponds to that of a solid spindle (without bore). Power is transmitted over the entire cross-sectional area with the corresponding tensile, compressive and torsional stresses.
Since the required processing effort is the lowest, the solid spindle is not only the simplest when it comes to manufacturing technology, but is also the most cost-effective design option.
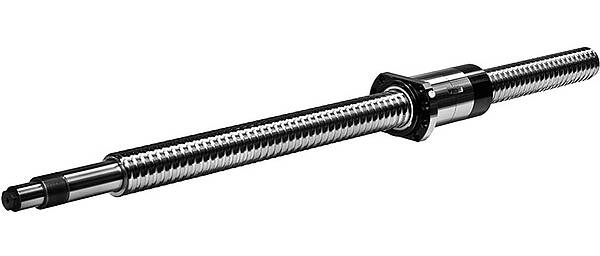
Hollow Spindles
If the ball screw shaft requires a central bore, for example for cooling or lubricating tasks, or different functional components need to be installed in this space, then the ball screw spindle can be designed as a hollow spindle. The spindle cross section in this case corresponds to that of a pipe with a corresponding wall. However, the pipe wall must at least be dimensioned so that the axial load and the torque can be transmitted without deformation and safely while taking the thread groove depth into consideration.
Advantages of Hollow Spindles
Using hollow spindles has various technical advantages. For example, the critical bending speed can be increased further by hollow boring the spindle. It is interesting that the critical bending speed constantly changes at otherwise constant spindle dimensions with an increasing internal diameter of the spindle. There is theoretically no saturation point from which the critical bending speed no longer increases. Of course, the exact production of such hollow spindles is problematic. The lower mass moment of inertia of hollow spindles is also advantageous.
If a fixed-fixed bearing is used, it is possible to use the bore of the hollow spindle for a cooling medium in order to keep the spindle temperature as constant as possible during the machining process. The necessary stretching forces are minimized here and pitch errors of the spindle are reduced as a result of thermal expansion.
If the spindle body has a fixed-fixed bearing and not the conventional fixed-loose bearing and is also hollow bored, then the loss of axial rigidity will be more than compensated for as a result of the hollow boring through the fixed-fixed bearing.
Hollow spindles have lower masses, lower rigidity and usually only lightly lower mass moments of inertia compared to corresponding solid spindles.
Since the inner contour of the hollow spindle is usually already made before the heat treatment, this is then also correspondingly hard (nitrided). Due to the lower masses, the temperature-related geometry changes of hollow spindles are larger during production. This leads to an increase in the diameter and above all to an extension of the spindle, which can also affect the thread pitch. Hollow spindles are usually much more processing-intensive and therefore more expensive to manufacture.
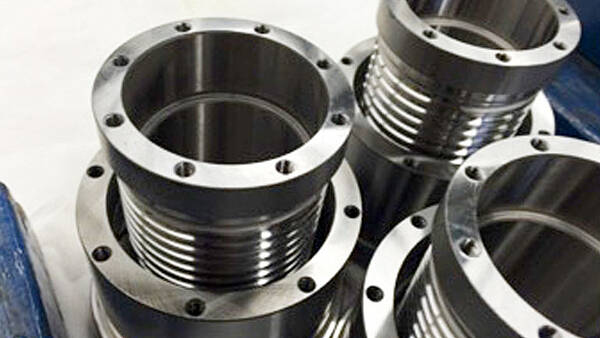
Spindles with Collars
The outer diameter of the ball screw shaft is usually the largest diameter from which all other shaft dimensions are worked out. It may be necessary under certain conditions to use larger diameters in individual shaft areas than the outer diameter of the ball screw. For example this may be the desire to have a larger contact shoulder for a spindle bearing and/or to achieve greater rigidity and stability in the spindle shaft. Such ball screw shafts are designated as ball screws with collars.
Because the spindle diameter is larger on one side, the ball screw nuts can only be mounted on one side with screw shaft with collars. Ball screws with collars can also have the larger spindle diameters in the spindle middle as well. With this design, the spindle then for example usually has a right-handed and left-handed ball screw alternately and is equipped with two nuts. The largest spindle diameter in the spindle middle is also used to accommodate a support bearing.
Since the outer diameter of the next larger nominal diameter often has to be selected as the output variable for reasons of material scheduling, the necessary machining effort to produce such a spindle is considerable. In addition, the collar is disruptive when grinding the ball screw.
Increased Production Effort
If the costs for this additional effort are greater than the additional material costs, then the production of a larger spindle is usually more economical. With larger spindles, however, it must be taken into consideration that the installation dimensions of the nut must also be increased and at the same time this increased space requirement must exist in the available installation space.
Sleeves and Rings as an Alternative
To circumvent the need for a spindle with collar design, sleeves or rings can be provided instead of the collar depending on the objective (e.g. with enlarged contact shoulder for the bearing). In these cases, the stable contact shoulder is made through these rings, which are installed after grinding the thread. These components can either be loosely threaded, adhered or shrunk.
The advantage of adhered support rings is that these can still be finely adjusted until right before the final adhesion. The adhesive Loctite 603 can usually be used for bonding. The bond can also be easily released again with the corresponding addition of heat. To avoid the adhesive getting into the loaded turns or into the nut, it must be ensured during bonding that only the bore surface and not the front face is wetted with adhesive.
With shrunk support rings, it must be ensured that the ring is applied fully to the installation edge without a gap, since it can no longer be aligned or displaced later on. It is only possible to disassemble the ring by using large forces and it usually cannot be done without destruction. Due to the significantly higher production costs, screw shafts with collars should only be used when it is absolutely technically necessary and there is no practical alternative solution.
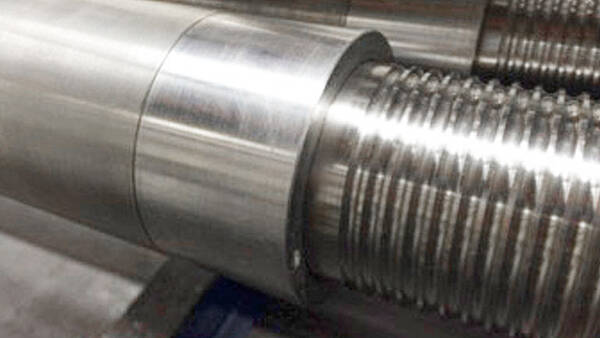
Coupled ball screws for Excess Lengths of up to 25 m
The maximum length of a ball screw shaft is usually limited by the availability of the raw material and the production capabilities (e.g. grinding, nitriding). To be able to produce longer spindles if required, it is also possible to permanently couple two ball screws. Two finish-ground connecting screws are aligned here so that the threads run exactly into each other. The screws are used to connect the mating faces of the 2 ball screw shafts. The rigidity at the joint is additionally reinforced by the opposite pitch of the 2 connecting screws (right and left-handed).
The spindles aligned in this way are form-fit by means of a coupling point specifically developed for this purpose. If the travel deviations of both spindle pieces are almost identical, coupled spindles normally do not result in any notable reductions in quality. Theoretically, any length of spindle can be produced through several coupling points.
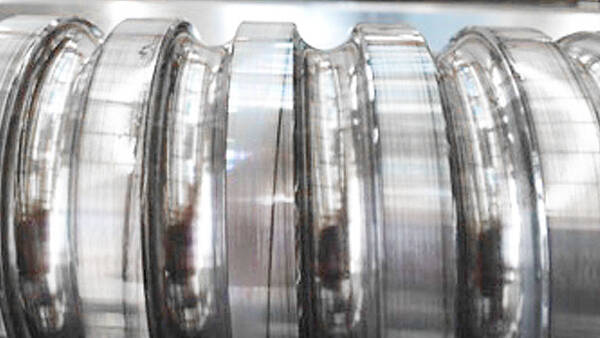
Exact knowledge of the ball screw use and the existing distribution of forces is very important when designing and evaluating the coupling point. The coupling point is usually only loaded with the occurring axial force for ball screws with driven nuts. If the spindle is driven, the drive torque in the spindle is also added as a load in addition to the axial force.
Please describe your application case to us. Our experts will advise you individually.
Applicability
Coupled ball screws are normally only used in a horizontal position. Due to the possible axial tensile load, and for safety reasons A.MANNESMANN does not produce vertically suspended ball screws in a coupled design.
Thread Length
The thread length of a ball screw is decisive for the total length of a ball screw shaft. It consists of the useful travel, the runouts on both sides and the length of the nut body. The useful travel lu is the maximum possible travel of the nut through which the required accuracy is applicable. It should be dimensioned larger than the structurally intended nominal travel of the axis and is usually limited by end stops and/or limit switches. The pitch-dependent runout le has no accuracy requirement, since it is normally not traveled. The installation lengths for the wiper may also need to be considered for the nut length l2.
Spindle Details
In order to completely ensure the functionality and quality of a ball screw , various details are to be taken into consideration during ball screw shaft production that can only partially or not at all be assigned to the ball screw. These include, for example:
- Bearing journals
- Support journals for drive components
- Thread runouts
- Undercuts
- Centering
- Mounting thread
- End tapped holes
- Spanner flats
- Rotary encoder connections
Accuracy of Screws
The accuracy of a ball screw is determined by the thread pitch and the associated path deviation based on the travel. The path deviation of the nut is always less than the pitch error in the ball screw shaft, since the pitch tolerance of the nut somewhat dampens the effect of the spindle pitch error. This accuracy ultimately decides the usability of the ball screw as a positioning or transport ball screw.